Testing Stability of a 3-D Printed Super Alloy under Extremes
Department of Energy, NNSA Center of Excellence CAMCSE researchers have published their latest research in Scientific Reports detailing a high-resolution electron microscopy study on a pressure-treated 3-D printed super alloy known for its unusually high strength and high ductility.
The published study was led by UAB and includes participants from the University of Massachusetts-Amherst, the University of California-Irvine, and the University of Notre Dame. The real secret behind superlative mechanical properties of 3-D printed super alloys is the nanostructure arrangement of two different crystalline structures that are present in this material. The crystalline structures involved are simple cubic structures (body-centered cubic and face-centered cubic), but their nano-layer arrangement achieved by 3-D printing resist deformation. Under applied high pressures, body-centered cubic transforms to face-centered cubic, however, stability of nano-layered structure required innovative electron microscopy studies.
PI of CAMCSE Yogesh Vohra says that these results are significant as they utilized state-of-the-art Focused Ion Beam technology to extract a few-nanometers thick sample from the transformed sample that was compressed in a UAB diamond anvil cell device (Figure below). One nanometer (nm) is one billionth of a meter; for example, human hair diameter is approximately 80,000 nm. The crystalline structure transformation was confirmed by x-ray diffraction using HPCAT's facility at the Advanced Photon Source, Argonne National Laboratory in Chicago. The electron microscopy was performed on a nanometer-thick sample to extract the crystal structure and nanostructure morphology induced by application of high pressure. The electron microscopy confirmed the irreversibility of the transformation and quite surprisingly the nano-layer arrangement remained unperturbed even after exposure to extreme pressure of 30 GPa (300 times the pressure at the deepest spot in the ocean) The published work will become part of PhD thesis of graduate student Andrew Pope (lead author on this paper). For more details, see: https://www.nature.com/articles/s41598-024-67422-x
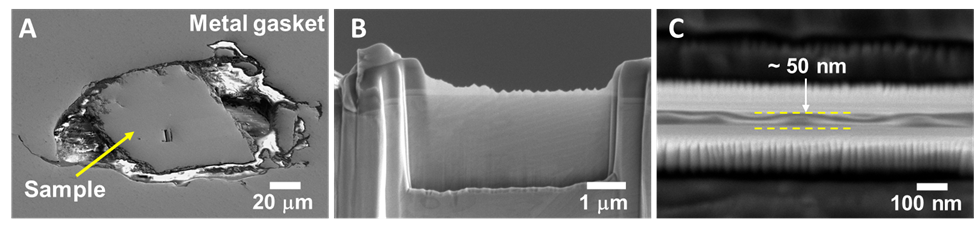
The overall goal of CAMCSE is to understand how additively manufactured (3-D printed) material performs under extremes of pressures, temperatures and high velocity impact or shock compression. The fundamental understanding of phase changes and nano structuring in 3-D printed superalloys will help us design better materials for use in extreme environments. For more information about this NNSA Center of Excellence, see https://sites.uab.edu/camcse/